Controlling the Greenhouse Environment
HGA-00336 View this publication in PDF form to print or download.
There are many opportunities and approaches for producing crops in greenhouses. In the planning phase, decisions need to be made on greenhouse layout and design. A suitable location needs to be identified before the greenhouse can be constructed. When the greenhouse space becomes available and suitable crops, varieties and growing systems have been determined, focus needs to be directed to maintaining and controlling a suitable greenhouse environment. The greenhouse as a controlled environment is an opportunity for Alaska gardeners and commercial producers to combine optimal temperature, light and humidity conditions with proper watering, fertilization and management to produce top-quality plants of the selected crops.
Heating
Heating is required during the winter half of the year and may enhance summer plant growth by keeping greenhouse temperatures above ambient levels. Greenhouses in Alaska are often operated seasonally because of the high energy costs for heating and electricity. Nationally, heating constitutes 65 to 85 percent of annual energy cost for a year-round commercial greenhouse (Runkle and Both, 2011).
As solar heat in the form of light enters the greenhouse, objects absorb it and reradiate it into the greenhouse environment (the greenhouse effect). Glass or rigid plastic greenhouse covering materials are optimal for trapping as much as 96 percent of thermal radiation, while single layer polyethylene is less efficient, with more than 50 percent of the thermal radiation escaping. Polyethylene plastic that contains radiation-absorbing (IR-absorbing) materials improves retention of thermal radiation by approximately 20 percent (Bartok, 2001). To improve heat retention, IR-polyethylene plastic should be considered, although local availability may be limited (check with local commercial greenhouse operators). Inflated double-layered polyethylene plastic is commonly used in Alaska and is 40 percent more efficient in retaining heat than single-layer polyethylene (Nelson, 2012). In either case, the polyethylene plastic should contain a UV inhibitor or it is unlikely to last more than one season. If on a tight budget, check with local Alaska greenhouse operators who use UV-inhibited polyethylene plastic. Used plastic can often be purchased for a fraction of the original cost and provides several years of excellent service to a greenhouse gardener.
Heat loss from a greenhouse occurs through convection, conduction or radiation. Convection is the transfer of heat through circulation and mixing of warm air with colder air. Conduction is the movement of heat between or through objects such as a metal rod or a greenhouse covering material. Radiation is the movement of heat from a warm to a colder object without the need for a medium such as air (convection) or direct contact between or through objects (conduction).
When the air outside is colder, a greenhouse loses heat through conduction across the covering material. The amount of heat loss depends on the conductive characteristics of the covering material. Outside air in contact with the warmer covering material is continuously mixed to remove heat through convection. Air exchange or infiltration through greenhouse cracks, small openings and gaps around doors, equipment and other greenhouse features, is another form of convective heat transfer. Although radiation is important for solar heating of a greenhouse, thermal radiation is of minor importance for heat loss from a greenhouse. Wind, on the other hand, significantly increases heat loss, and the greenhouse heating requirement doubles as wind speed goes from 0 to 15 miles per hour.
The type of covering material, the cloud cover, and the inside and outside ambient temperatures determine the amount of heat lost from a greenhouse. Condensation inside a polyethylene covering may reduce heat loss 50 to 75 percent. Unfortunately, condensation, in addition to reducing thermal loss, also limits transmission of light and solar radiation. Since most greenhouses in Alaska have roofs with rather steep slopes, or pitch, to facilitate the shedding of snow, condensation is not often a major issue.
Heater Selection
Gas hot air heaters come in a wide variety of configurations and fuel options. Natural and bottled gas hot air heaters are some of the more economical and efficient types of heaters available for Alaska greenhouses. Unit heaters, mounted on the wall or freestanding, have proved to have fast response times and are economically priced and low-maintenance heating sources for Alaska greenhouses.
Hot water heaters and boilers that provide radiant, floor and bench heat continue to gain acceptance for use in greenhouses, as well as in homes and garages. Gas and electrically fired systems are available and these heating sources provide good, uniform heating. The boiler units should operate as a closed system. Standard home hot water heaters may also be used, and in some cases they offer a dual purpose by producing hot water for heating the air and tempered tap water for watering plants. These systems must be protected from freezing and winterized by draining water and blowing air through all lines. While not as responsive to rapid temperature changes as hot air heaters, hot water baseboard and radiant floor heaters have multiple temperature zone capabilities to provide more uniform temperatures within a greenhouse. Hot water heaters are also better than hot air heaters at maintaining lower uniform temperatures in the spring and fall.
Electric heaters are more costly to run but they are usually inexpensive and may work well for supplementing heat during a few spring and fall nights or a cold spell during the growing season. Utility, baseboard or infrared electric heaters are all suitable for warming a greenhouse. Since infrared heaters heat objects that re-radiate heat to the surrounding air, they can be more efficient than electric hot air heaters. Research at the University of Connecticut found electrical cost savings of 25 percent when heating an 8- by 12-foot greenhouse using an infrared heater versus an electric hot-air heater (Bartok, 2000). On the other hand, because infrared heating tends to warm the surface of objects and plants, soil temperatures stay cooler.
Wood heat can be used as the main or supplemental heating source for greenhouses. Safety may be an issue since a burning wood stove should always be attended. Combining wood heat with a nighttime gas or electric system is one option. Heat regulation is more difficult, however, even with a thermostatically controlled wood stove since the fire does not automatically restart if it goes out and heat is needed. However, a larger air mass buffers against rapid changes in temperature, so wood heat is easier to manage for desired temperatures in a larger greenhouse as opposed to a smaller greenhouse, which will heat up faster and cool off faster, making it more difficult to maintain a desired temperature.
Pellet stoves, while expensive, are worth consideration. Pellet stoves burn manufactured dried wood pellets rather than cordwood. They can be controlled by a thermostat and are often semi-automated. Pellets are moved to the stove from a storage area using an electric auger. Local availability of pellets may be an issue or justification.
Fuel heaters (oil, kerosene, white gas or diesel) are not recommended for use in greenhouses unless adequate ventilation is provided. However, with frequent cleaning and maintenance, portable kerosene heaters that burn K-1 grade kerosene may be used successfully. For smaller greenhouses, kerosene heaters are especially well suited for emergency situations. Oil-fired furnaces are often too large to fit into the greenhouse design and structure. If used to heat other buildings as well as the greenhouse, such as a home, work area or storage facility, an oil-fired boiler can be advantageous.
When selecting a greenhouse heating system, the amount of heat for maintaining the desired greenhouse temperature needs to be known. Greenhouse covering materials are rated for their heat conductive properties. The U-value is a measure of heat transmission through a material. The higher the U-value, the less insulation the covering material provides. Table 1 lists U-values for some popular greenhouse covering and wall materials. In contrast to the U-value, the R-value is the insulative coefficient of a material and the inverse of the U-value. By matching the greenhouse heating requirement (calculated as the hourly heat loss) with the heater output in Btu/hour, a correctly sized heater can be chosen (make sure to use heater output and not the input value). British thermal units (Btu) are commonly used to measure energy and represent the amount of heat required to raise the temperature of one pound of water one degree Fahrenheit.
Using the information in Table 2 and the square footage of the greenhouse (length × width), the heating requirement can quickly be estimated. For example, a 12-foot by 16-foot freestanding greenhouse has a floor area of 192 square feet. If heat is supplemented all winter and the greenhouse has a single-layer covering (Zone B: -30°F minimum), a heater providing 69,120 Btu/hour (192 × 360 Btu/square foot) is needed. If heat is only provided from April through October, approximately 23,040 Btu/hour will be needed (192 × 120 Btu/square foot for Zone G).
Greenhouse glazing or wall materials | U-value: (Btu/h x °F x sq ft) |
---|---|
Glass - single | 1.2 |
Plastic film - single | 1.25 |
Fiberglass reinforced plastic - single | 1.2 |
Polycarbonate - single | 1.2 |
Glass – single w/ thermal blanket | 0.5 |
Plastic film - double | 0.8 |
Acrylic or polycarbonate - double | 0.6 |
Plastic film – double w/ thermal blanket | 0.4 |
Standard concrete blocks, 8 inches | 0.5 |
Poured concrete, 6 feet | 0.75 |
Softwood lumber, 1-inch thick | 1.10 |
Concrete block, 8 inches + 2 inches foamed urethane board | 0.07 |
Concrete block, 8 inches + 2 inches foamed polystyrene board | 0.10 |
Poured concrete, 6 inches + 2 inches foamed urethane board | 0.07 |
Wood-framed wall with 1.5-inch thick urethane board | 0.12 |
Perimeter, uninsulated | 0.8 |
Perimeter, insulated: 2-inch foam board, 24 inches deep | 0.4 |
Source: Greenhouses for Homeowners and Gardeners (NRAES-137)
Table 2. Estimated Heat Requirements in Btu/Square Foot of Surface Area | |||||||
Zone | |||||||
---|---|---|---|---|---|---|---|
A | B | C | D | E | F | G | |
-40°F | -30°F | -20°F | -10°F | -0°F | 15°F | 30°F | |
Lean-to Greenhouse | |||||||
Single glazing | 370 | 330 | 290 | 250 | 210 | 175 | 140 |
Double glazing | 250 | 220 | 190 | 160 | 130 | 100 | 70 |
Freestanding Greenhouse | |||||||
Single glazing | 400 | 360 | 320 | 280 | 240 | 180 | 120 |
Double glazing | 250 | 225 | 200 | 175 | 150 | 110 | 85 |
*Zone. The table assumes a 60°F inside night temperature and the following minimum temperatures for your given area; individual locations may have temperatures lower than this. In borderline locations, select the colder zone. Source: Adapted from Greenhouses for Homeowners and Gardeners (NRAES-137). |
A more accurate method (Kramer, 2013) for calculating heat loss in a greenhouse is the formula HL (heat loss) = SA (surface area of the greenhouse covering) × U (heat loss factor of covering material) × TD (difference between highest inside and lowest outside temperature). Examples 1 and 2 illustrate the use of this formula for calculating the heat loss in a lean-to greenhouse (Example 1) and in a freestanding greenhouse (Example 2).
Comparing the calculated heating requirements, the simple method (Table 2) resulted in an overestimation of approximately 6,000 Btu/hour for the 12-foot by 16- foot greenhouse. The example of the lean-to greenhouse also results in a similar overestimation using the method in Table 2. Although the estimates differ, the simpler formula is still a useful tool for making a rough assessment of the heating requirements for various types of greenhouses.
Planning for abnormally low outside temperatures can make the difference between saving or losing a crop and protecting the greenhouse structure. In Alaska, a slightly oversized heater is always better than an undersized heat source. A backup system is crucial for year-round commercial greenhouses in Alaska, but is rarely an issue for seasonal greenhouse gardeners. Multiple heater systems are often set up to efficiently use one heater as the primary heating source with backup heaters for periods of extremely low outside temperatures, primary heater failure or scheduled maintenance.
Compartmentalizing plant germination and production areas in the greenhouse also reduces the need for heat. Alaska greenhouse gardeners often start seedlings under fluorescent or other types of lights in a garage or basement and transfer them to the greenhouse later, which delays the demand for energy. In large commercial greenhouses, the placement and orientation of convection tubes within the greenhouse can significantly affect the efficiency and distribution of heat. Air movement and heat distribution are of less concern in smaller, seasonally operated greenhouses.
Solar heat is an alternative heat source derived from the sun in the form of solar radiation and captured in purposely built storage structures inside the greenhouse. The stored energy reradiates into the greenhouse to keep it warm during the night. Table 3 summarizes commonly used options and materials for heat storage in solar greenhouses. In a properly built and oriented solar greenhouse, sufficient energy can be captured during a sunny day in March to heat the greenhouse for two additional days (Bartok, 2000).
The design of a solar greenhouse differs from the design of a normal greenhouse. The major difference is the orientation in relation to the sun. To maximize exposure to the sun and its available energy, a solar greenhouse should be oriented to within 20 degrees of true south. The ridge of the greenhouse should run east-west so that a long wall gets southern exposure to optimize the reception of solar radiation. The slope of the greenhouse roof is also critical. To estimate the slope needed to capture a winter sun’s energy, use the latitude plus 15 degrees. In Alaska, the desired roof angle for winter conditions is between 75 and 80 degrees. A shallower slope of 50 to 60 degrees is appropriate for capturing spring and fall sun.
Example 1. 12-x 16-foot lean-to greenhouse (adapted from Greenhouses for Homeowners and Gardeners, NRAES-137)
Surface area:
End walls: 2 x 6 ft. x 12 ft. = 144 sq. ft.
Sidewall: 6 ft. x 16 ft. = 96 sq. ft.
Peaks (endwalls) = 2 x 0.5 x 12 ft. x 6 ft. = 72 sq. ft.
Roof: 13.4 ft. (a2 + b2 = c2) x 16 ft. = 214.4 sq. ft.
Total: 526.4 sq. ft.Heat Loss (HL) = Surface Area (sq. ft.) of greenhouse (SA) x U factor (U) x Temperature
difference between minimum outside and 60°F inside (standard) (TD)
Given:
SA = 526.4 sq. ft.
U-value (single layer polycarbonate – Table 10) = 1.2
TD= 60°F [desired inside temperature] + 30 (-30°F) = 90
Heat Loss = 526.4 x 1.2 x 90 = 56,851 Btu/hr.
Example 2. 12- x 16-foot freestanding greenhouse (adapted with permission from Greenhouses
for Homeowners and Gardeners, NRAES-137).
Surface area:
Ends: 2 x 6 ft. x 12 ft. = 144 sq. ft.
Sides: 2 x 6 ft. x 16 ft. = 192 sq. ft.
Peaks (end walls): 2 x 0.5 x 12 ft. x 3 ft. = 36 sq. ft.
Roof: 2 ft. x 6.7 ft. (a2 + b2 = c2) x 16 ft. = 214.4 sq. ft.
Total: 586.4 sq. ft.
Heat Loss (HL) = Surface area (sq. ft.) of greenhouse (SA) x U
factor (U) x Temperature difference between minimum outside and 60°F inside (standard)
(TD)
Given:
SA=586.4 sq. ft.
U-value (single layer polycarbonate – Table 10) = 1.2
TD= 60°F [desired inside temperature] + 30 (-30°F) = 90
Heat Loss = 586.4 x 1.2 x 90 = 63,331 Btu/hr.
Except for the transparent covering material on south-facing sections of the greenhouse, parts of the roof and wall areas are insulated in a solar greenhouse. At night, an insulation blanket or other type of material is unrolled to retain heat. Supplemental heat may be required in a solar greenhouse when the weather is cloudy and solar radiation is limited.
Shading
Intense summer sun and the extremely long days in Alaska require shading for temperature control and optimal plant performance in the greenhouse. Table 4 offers shading suggestions for an assortment of common ornamental plants grown under northeast United States environmental conditions. While overall demand for shading may be higher in the Northeast, shading is essential during the warmest part of clear, sunny Alaska days to maintain the desired temperatures or cool the greenhouse.
There are two distinct categories of shading materials for greenhouses: shading compounds (or diluted latex paint) applied to the outside greenhouse covering material or fabrics draped over or used as a curtain inside the greenhouse. There are many installation options and systems that can be tailored to the greenhouse type and needs for shading. Check with a greenhouse equipment supplier for shading systems that will work for your needs. Greenhouse covering materials have various light transmission values, and those with lower transmittance provide some built-in shading that should not be ignored. Table 5 has light transmission values for some examples of greenhouse covering materials.
Water/Air Temperature | Btu Stored | |
---|---|---|
1-Gallon Jug | 5-Gallon Jug | |
60ºF | 83 | 417 |
70 | 167 | 834 |
80 | 250 | 1,251 |
90 | 334 | 1,668 |
30-Gallon Barrel | 55-Gallon Barrel | |
60ºF | 2,500 | 4,590 |
70 | 5,000 | 9,170 |
80 | 7,500 | 13,760 |
90 | 10,000 | 18,340 |
Concrete/ Concrete Block | Brick | |
60ºF | 224/cubic foot | 271 |
70 | 448 | 542 |
80 | 672 | 813 |
90 | 896 | 1,084 |
Rocks in Crate Under Bench | Stone in Floor | |
60ºF | 220/cubic foot | 240/cubic foot |
70 | 440 | 480 |
80 | 660 | 720 |
90 | 880 | 960 |
Adapted from Greenhouses for Homeowners and Gardeners (NRAES-137). Originally published in Bartok, John W., D.S. Ross, J. White, W.J. Roberts, C.A. Aldrich, and R.A. Parsons. 1982. Solar Greenhouses for the Home (NRAES-2). Ithaca, N.Y.: Natural Resource, Agriculture and Engineering Service (out of print).
Suggested degree of shade | Type of plant |
---|---|
25–35% | Geraniums, chrysanthemums, snapdragons |
45–50% | Bedding plants, lilies, caladiums |
50–55% | Azaleas, begonias, gloxinias, African violets, poinsettias |
55–60% | Orchids, pachysandra, ivy, bromeliads, ficus |
60–65% | Rhododendron, dieffenbachia |
70–75% | Fern, philodendron, dracaena |
75–80% | Palms |
Source: Greenhouses for Homeowners and Gardeners (NRAES-137)
Glazing | Percent Light Transmittance |
---|---|
Glass-single | 85–95 |
Glass-Factory sealed double | 70–75 |
Polyethylene-single | 80–90 (new) |
Polyethylene-double | 60–80 |
Polyethylene-corrugated high density | 70–75 |
Laminated acrylic/poly film-double | 87 |
Impact modified acrylic-double | 85 |
Fiber reinforced plastic | 85–90 (new) |
Polycarbonate-double wall rigid | 83 |
Source: Adapted from: Bellows, B. 2011. Solar Greenhouses. ATTRA National Sustainable Agriculture Information Service.
Cooling
Need for air movement in the greenhouse
There are two primary reasons airflow is necessary in greenhouses: (1) to remove excess heat through ventilation as the temperature rises, replacing hot air with cooler air, and (2) to control relative humidity and carbon dioxide within the plant canopy. A single system can serve both needs in smaller greenhouses, while separate exhaust and circulation systems are common in larger-sized greenhouses. Separate systems need to be carefully coordinated and adjusted to work together instead of counteracting each other Air movement systems range from simple, do-it-yourself arrangements to professionally designed, installed and integrated computer controlled systems.
Temperature Control Systems (Ventilation)
As the sun warms the greenhouse, temperature rises rapidly. Without a method of removing excess heat, the temperature may increase to levels detrimental for crop growth. The purpose of the ventilation system is to prevent temperature increases and heat buildup by replacing the hot air with cooler outside air.
Smaller greenhouses can be adequately ventilated by leaving doors and windows open or by removing sections of the covering (Picture 1). By properly orienting the greenhouse to take advantage of local wind patterns, summer winds may be captured and vented into the greenhouse for cooling For medium and large-sized greenhouses, however, air movement and ventilation needs must be met with a combination of active and passive systems.
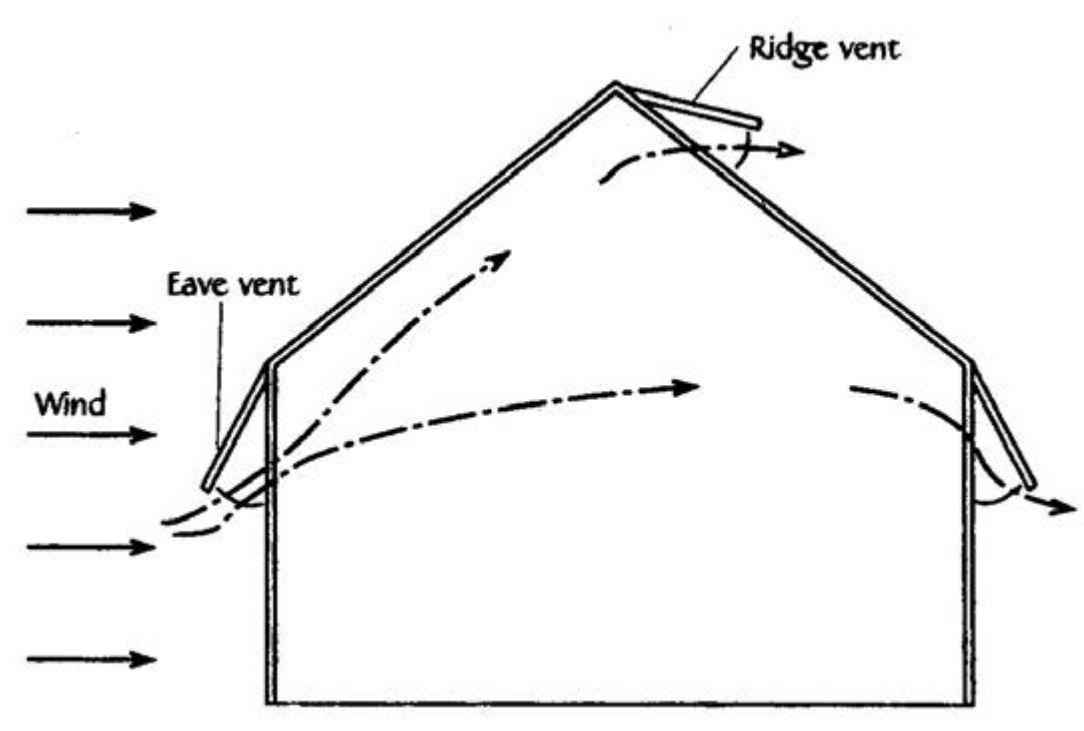
Passive ventilation systems operate on the principle that air expands when heated, increasing the pressure in the greenhouse. To release pressure, air is pushed through vents or other openings in the structure and replaced with air pulled or pushed by wind through other openings in the greenhouse. In Alaska, the greenhouse air heats up rapidly during days with intense spring and summer solar radiation. With a passive ventilation system, hot air flows out of vents positioned in the greenhouse roof or end walls. Cooler air is brought in through side vents (or other uncontrolled openings) to replace the hot air and lower the interior temperature (Figure 1; Bartok, 2000). Vents along part or the entire length of the roof ridge can be an efficient greenhouse ventilation system (Picture 2). The passive ridge-vent system works well when combined with adequately sized vents in side or end walls for air intake and is often found in commercial greenhouses.
One of the least expensive greenhouse ventilation systems is the roll-up or drop-down wall design. This system uses plastic sheeting for the walls only or for the entire greenhouse. Commercial-grade greenhouse film with a UV inhibitor should be used for longevity. Low-budget seasonal greenhouses with a wooden or plastic pipe frame often incorporate the roll-up or drop-down wall system to achieve adequate ventilation (Picture 3).
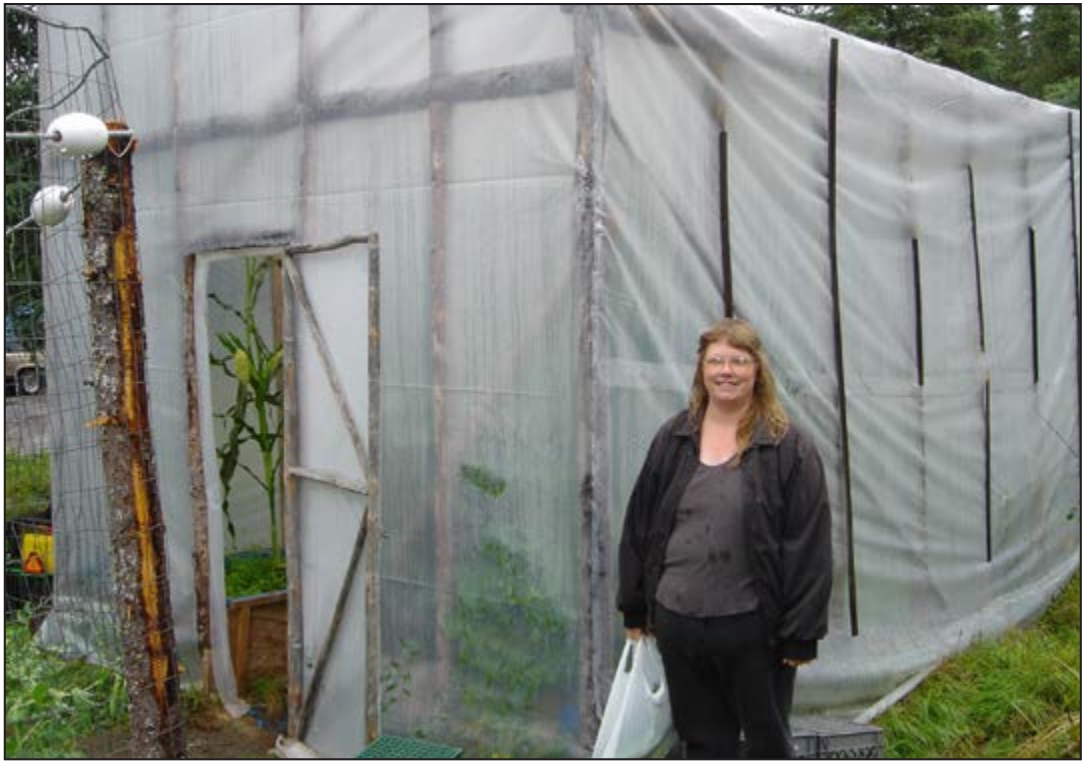
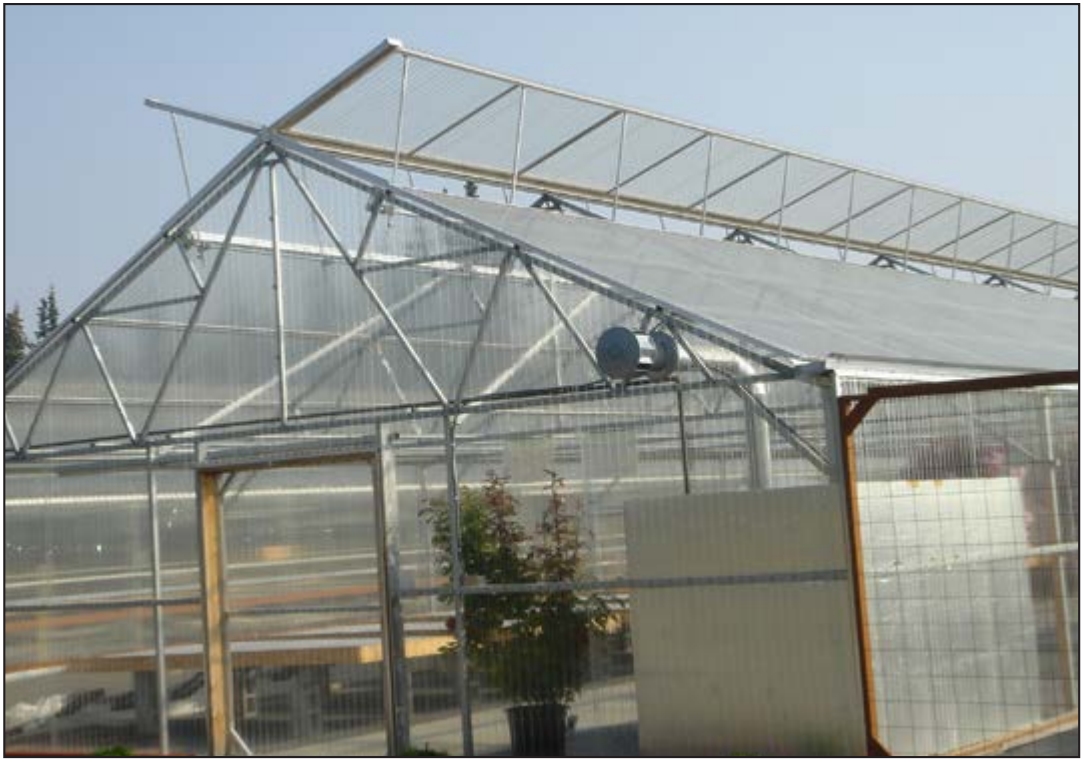

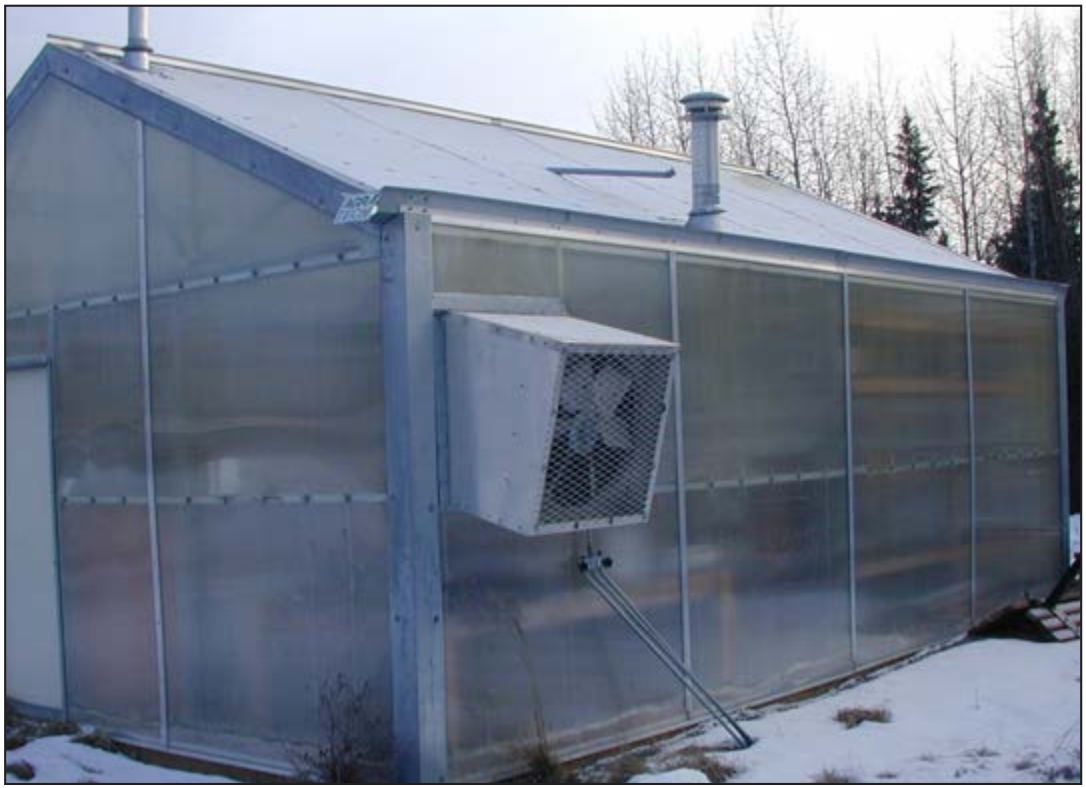
As greenhouse size increases, the need for ventilation usually increases too. Exhaust fans combined with adequate air-intake are needed to enhance and maintain temperature control. Mechanical systems with variable speed fans, motorized louvers (dampers) and adjustable vents are available for sufficient air movement and ventilation. Computer programs coordinate and control the various components in these systems to optimize ventilation and airflow.
Fans
Fans either pull fresh air into a greenhouse or exhaust greenhouse air to the outside with replacement fresh air entering through vents or other openings. Although there is no special preference, most commercial greenhouse operations use fans to exhaust air with replacement air pulled through vents from the outside.
In a freestanding greenhouse, fans and vents are usually installed in opposite walls (Picture 4). Placement in end walls allows for good airflow along the length of the greenhouse and across the crops. Positioning fans to exhaust in the direction of prevailing winds is desirable since a fan exhausting air against outside wind pressure requires more force and energy. Greenhouse ventilation is 10 percent more efficient when vents and fans are oriented so that air is pulled in and exhausted out of the greenhouse with the prevailing wind instead of against it.
The placement and opening of doors can enhance or hinder the operation of fans. An open door in an end wall opposite the exhaust fans encourages airflow through the greenhouse. Air always follows the easiest path, and air entering a door opening close to an exhaust fan will escape through the fan without travelling across the greenhouse production area. In this situation, the exhaust fans are not effectively pulling air through the vents, which results in uneven and insufficient air movement for cooling the greenhouse.
Vents and exhaust fans are often effective cooling systems in moderate-sized greenhouses. In greenhouses 150 feet long or longer, the cooling efficiency diminishes. The incoming air heats up as it travels across the greenhouse. With a long distance between air intake and exhaust, the air temperature increase is too high for cooling the entire greenhouse.
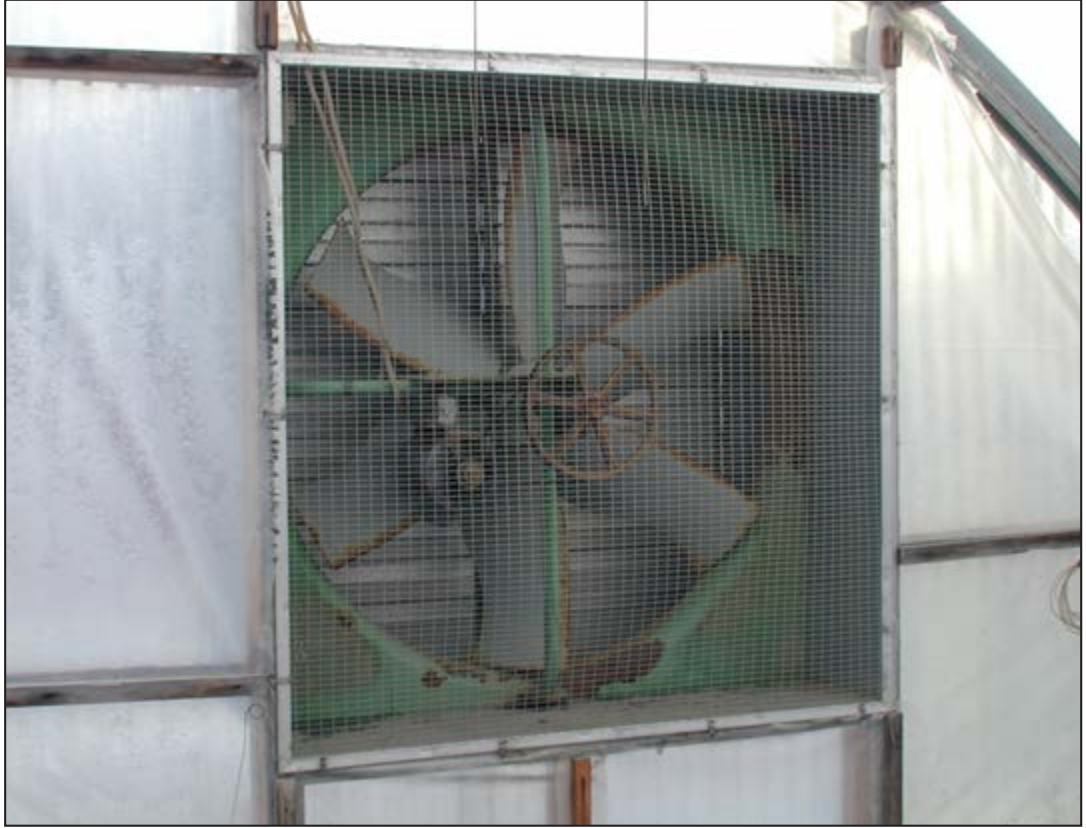
The capacity of the exhaust fan needs to be correlated and matched to the intake of air through louvers or vents. Fan capacity is a measure of the volume of air a fan can move and is expressed in cubic feet per minute (cfm). The fan output is recorded and indicated as cfm under no air resistance (free air) and as one or several static pressure values measured in inches of water column. The static pressure value takes into account friction created by, for instance, air passing through a louvered vent. The manufacturer should provide technical specifications for the fan capacity at various static pressures. Fan capacity ratings at ⅛ inch (0.125 inch), rather than no static pressure, should be used for Alaska greenhouses. If insect screening or evaporative cooling pads are used, fan ratings of ¼ inch (0.250 inch) or greater static pressure need to be considered. Typical fan performance under two static pressure values are summarized in Table 6.
For Alaska, an acceptable standard of air movement is 12 cfm for each square foot of greenhouse floor area. As an example, Picture 4 shows a greenhouse measuring 16 feet by 24 feet, with a floor area of 384 square feet. Multiplying 384 square feet by 12 cfm per square foot results in 4,608 cfm, the required fan capacity to adequately ventilate this greenhouse using an exhaust fan and louvered vent system. Since the need for ventilation varies throughout the seasons, consider two-speed or variable-speed fans (Picture 5). Slow-speed fans are used for internal air circulation (horizontal air flow) while higher capacity airflow is required for exhausting heat and cooling the greenhouse.
Prop diameter | Air Flow (cfm) | |
---|---|---|
Variable Speed | 0 in. SP | 0.125 in. SP |
10 in. | 585 | 285 |
12 in. | 800 | 470 |
16 in. | 1095 | 720 |
18 in. | 1880 | 850 |
20 in. | 2830 | 2255 |
24 in. | 3240 | 2485 |
Single Speed | ||
18 in. | 2590 | 2190 |
20 in. | 2955 | 2450 |
20 in. high speed | 3635 | 3113 |
24 in | 3270 | 2515 |
24 in. high speed | 3970 | 3240 |
30 in. | 6075 | 4195 |
30 in. | 6075 | 4195 |
36 in. | 8225 | 6480 |
Two Speed | ||
24 in. | 3985/3760 | 3255/2995 |
Source: Adapted from Grainger, Inc. 2014. Catalog No. 405, p. 4094.
Vents
When using exhaust fans, vents are needed for air intake. If air is exhausted without an adequate source of replacement air, the fans will either wear out quickly or air will be pulled through existing or newly created leaks in the greenhouse structure.
Regardless the equipment of choice, the vent(s) on the opposing end of the greenhouse must work in conjunction with the fans. Smaller vent units may be pushed open by the fan-generated air pressure. Larger vents are motorized and synchronized to the exhaust fans through a control system. Air flows easily through motorized systems since the moving air does not have to hold the vents open. In smaller greenhouses, vents may open and close with mechanisms that use the heat-induced expansion of specific liquids or waxes. These mechanisms do not use motors or thermostats and work with vents that weigh less than 10 to 15 pounds.
To provide adequate airflow and ventilation, the surface area of the vent openings should be at least 1.25 times the area of the fans (Table 7) or 1.5 square feet per 1,000 cfm of fan capacity (Bartok, 2000). For optimum efficiency, roof vents should be 15 to 20 percent of the floor area.
Fan Size | Minimum Vent Area |
---|---|
16 in. | 251 sq. in. |
18 in. | 318 sq. in. |
20 in. | 393 sq. in. |
24 in. | 566 sq. in. |
30 in. | 884 sq. in. |
Vents opening downwind and fans exhausting with prevailing winds significantly improve the cooling capacity of a greenhouse (Figure 1; Bartok, 2000). However, while downwind venting offers optimum ventilation, orientation, logistics and location also need to be considered when planning and designing a greenhouse.
Ventilation Placement
Most ventilation systems are designed to release warm air at the top of the greenhouse with the cool air intake placed closer to ground level. In Alaska, this strategy may not work because cool air at crop height may damage or even freeze the plants. The air intake needs to be well above the height of the crops during spring, fall and winter conditions to allow the cold, fresh air to mix with warmer greenhouse air before coming in contact with the plants. Traditional ventilation placement maximizes cooling during the warmer parts of the growing season. For best results during summer months, windward wall vents should be located at approximately plant canopy level.
Air Circulation
In photosynthesis, plants use carbon dioxide and produce oxygen. The gas exchange takes place through tiny pores in the leaves called stomates. Air movement is sufficient to mix oxygen and carbon dioxide with the surrounding atmosphere under outdoor field conditions. In a greenhouse, on the other hand, limited air movement can result in an imbalance of increased oxygen and low levels of carbon dioxide in the boundary layers around the leaves. Lack of air movement and limited carbon dioxide will slow photosynthesis and overall crop growth.
Good air circulation is also important in the greenhouse to manage the relative humidity in the air. Plants continuously transpire, increasing the moisture around the leaves. Warm air can hold more water vapor than colder air, and as the temperature drops to the dew point, the moisture in the air will condense into liquid water. High relative humidity and the formation of water droplets on the foliage create conditions that are favorable for plant diseases. Mixing humid air with dry air decreases the risk for condensation and outbreaks of diseases.
During the winter, air is often circulated within the greenhouse with limited or no outside air exchange. Continuous air movement keeps the greenhouse temperature more uniform, decreases relative humidity in the canopy and on leaf surfaces, and maintains gas exchange between the boundary layer and the surrounding air. Fans and vents should be installed to direct the airflow across and through the canopy rather than under benches or along walkways.
In small greenhouses (less than 300 square feet), a continuously running furnace, with heat on or off, can provide sufficient air circulation. Dedicated 8- to 16- inch horizontal airflow (HAF) fans are recommended for larger greenhouses. HAF fans improve plant health, algae management and control of condensation to make the investment cost effective (Bartok, 2000). Research has shown that suitable air circulation rates should be in the range of 40 to 100 cfm (Bartok, 2000; Nelson 2012). Lower airflow rates may result in humidity and carbon dioxide-related problems and airflow above 150 cfm may damage the plants.
HAF fans should be installed approximately 7 to 8 feet above the floor and placed about a quarter of the way along the length of the greenhouse. For every 50 feet of greenhouse length, add another circulating fan. Since the fans are rather exposed, good grills around the blades for worker safety are essential. The HAF fan capacity in cfm should be around one-quarter of the greenhouse volume. For example, a 20- by 50- by 8-foot greenhouse has approximately 8,000 cubic feet of volume (20 × 50 × 8 = 8,000 cubic feet). Dividing 8,000 cubic feet by 4 (one-fourth of the volume) results in 2,000 cfm of needed air movement. Table 8 offers fan size suggestions for circulating inside greenhouse air.
HAF fans are not needed when exhaust fans are running and operation should be coordinated through manual or controller management. Ceiling fans can be effective in greenhouses 400 to 800 square feet and at least 10 feet high. The installed fan blade should be at least 8 feet above the floor (Bartok, 2000). Oscillating fans that move air through the plant canopy can improve air circulation in smaller greenhouses.
Floor Area (sq. ft.) | Fan Diameter (in.) | Air Movement (cfm) |
---|---|---|
100 | 6 | 400 |
200 | 8 | 600 |
300 | 10 | 800 |
400 | 12 | 1,200 |
500 | 14 | 1,600 |
Adapted from Greenhouses for Homeowners and Gardeners (NRAES-137). Above recommendations provide approximately 50-100 cfm circulation rates for greenhouses up to 50 feet in length.
Humidity Control
A secondary role of the ventilation system is to eliminate excess humidity. If not properly vented, excess humidity condenses on the leaf surface where it can enhance disease problems. It can also condense on the greenhouse structure where it may reduce light transmission and encourage rust and/or rot of the structure itself. Greenhouse humidity levels can be reduced by removing the moist air around the plants and replacing it with the cooler and drier outside air.
Cultural Practices
High relative humidity is undesirable for growing most greenhouse crops. It is a contributing factor to a variety of plant diseases, including damping-off and Botrytis blight (gray mold). Proper planting dates, adequate spacing and morning watering (so that foliage can dry prior to lower night temperatures) are good cultural practices for managing relative humidity and controlling plant diseases.
Ventilation and Airflow
Proper ventilation and adequate internal greenhouse airflow are critical to the success of managing relative humidity in a greenhouse. Warm air holds more moisture than cool air. During a warm summer day, the internal greenhouse air accumulates moisture. As the evening outside temperatures cool, the internal air temperature drops, reducing its water-holding capacity until water condenses on greenhouse and plant surfaces at the dew point. To minimize this problem, air exchanges must take place to remove the moisture-laden internal greenhouse air and replace it with the drier outside air. If cool, this fresh air must next be heated to reduce internal relative humidity levels. Horizontal airflow helps mix warm and cool air together within a greenhouse to buffer the air from dropping below the dew point (Bartok, 2000).
Light
Supplemental lighting is usually not required in greenhouses in Alaska from May through September. To produce greenhouse crops during the winter half of the year, electrical lighting is essential. Supplemental lighting also improves plant growth during cloudy, low-light conditions and increases total daily light levels during short days of natural light. Another potential reason for supplementing light is to extend the day length or photoperiod to initiate or prevent flowering. The amount of light needed for extending the day length is usually considerably lower than the amount of light provided in support of overall plant growth. Comparisons among available light sources are offered in Table 9. Any lamp used for greenhouse lighting should have UL/CSA rating and approval.
Incandescent
The incandescent light bulb has been used for years as a light source. For plant growth, it was primarily used to extend the day length rather than as a grow light to enhance overall growth. Most of the electrical energy going into incandescent bulbs is released as heat rather than light. The traditional incandescent lamp is therefore being phased out and will not be available any longer in the United States. The decision to discontinue the use, manufacturing and sales of incandescent bulbs was initiated in 2012.
Halogen Incandescent
The halogen incandescent bulb is a more energy-efficient modification of the traditional incandescent bulb. Halogen bulbs are filled with halogen gas — usually bromine or compounds of bromine — in contrast to the vacuum or a low-pressure argon/nitrogen mixture in conventional incandescent bulbs. The change in the gas mixture allows for a higher operating temperature, resulting in a bulb with higher efficacy, intensity and color temperature. Depending on the wattage and type of gas mixture, the halogen version can be 30 to 60 percent more energy efficient (lumens per watt of electrical energy) than the traditional incandescent bulb. The lifetime of the bulb is often more than double the number of hours expected for a traditional incandescent bulb. Even with these modifications, the halogen incandescent bulb is also scheduled to be discontinued in the United States, as light emitting diodes (LEDs) are taking their place (see below).
Light Source | Efficacy* (lumens/watt)* | Lifetime (hours) |
---|---|---|
Incandescent | ||
Traditional | 10–17 | 750-2,500 |
Energy-Saving Halogen | 12–22 | 1,000–4,000 |
Fluorescent | ||
Straight Tube | 30–100 | 700–24,000 |
Compact | 50–70 | 10,000 |
Circline | 40–50 | 12,000 |
High-Intensity Discharge | ||
Metal Halide | 70–115 | 5,000–20,000 |
High-Pressure Sodium | 50–140 | 16,000–24,000 |
Light-Emitting Diodes | ||
Cool White LEDs | 60–92 | 25,000–50,000 |
Warm White LEDs | 27–54 | 25,000–50,000 |
*Amount of light as a ratio of the power required for producing it. Lumens: Units of measurement of light. One lumen = one foot-candle falling on 1 square foot of area. Source: Adapted from Office of Energy Efficiency & Renewable Energy, Energy.gov, https://www.energy.gov/energysaver/lighting-standards
Fluorescent
Fluorescent bulbs give off more uniform light than incandescent lamps. Fluorescent bulbs are available in 28- to 225-watt configurations and are often mounted in banks to cover larger growing areas. Home gardeners use fluorescent bulbs to start plants from seeds in late winter and early spring. Inexpensive fluorescent shop light systems work well for this purpose.
The 40- to 75-watt bulbs are suitable for germination and early seedling development that does not require the more expensive, higher-intensity, full spectrum “grow lights.” The key to using these low output lights is to place them within an inch of the plants so the plants can capture all provided light intensity (lumens). If they are not placed close to the plants, the result is stem elongation and weak, spindly plants that do not generally perform well. While houseplants, seedlings and low-light flowering plants can flourish under fluorescent lights, these lights fall short of the light requirements needed to produce most mature flowering and fruiting plants. White or aluminum foil reflectors may aid in directing the limited light intensities from these lamps (Table 10).
Fluorescent lighting has rarely been used in commercial greenhouses for producing mature flowering or fruiting plants because of its low-intensity output and the considerable shading the fixtures and reflectors create. In commercial operations, the primary use of fluorescent tubes has been to provide light over germination benches. The lamps are placed close to the benches; since only low light levels are needed for germination, fluorescent lamps are sufficient. As the seedlings develop and grow, they need more light than the fluorescent lamps can provide. To sustain rapid, high-quality growth, the seedlings need to be moved into a greenhouse with good natural or supplemental light.
Compact fluorescent lamps (CFLs) replaced incandescent bulbs in some applications. CFLs are often used alone or mixed with incandescent or halogen incandescent bulbs to extend the day length in some photoperiodic crops. Since CFLs are more energy efficient, using about 75 percent less energy than incandescent bulbs, the shift to CFLs for day length control was easily justified. LED alternatives are now available and are replacing fluorescent and CFLs light sources for plant growth.
Distance from Lamp (ft.) | Without Reflectors | With Reflectors |
---|---|---|
0.5 | 500 | 700 |
1.0 | 260 | 400 |
2.0 | 110 | 180 |
3.0 | 60 | 100 |
4.0 | 40 | 60 |
*fc= foot candles.
Source: Adapted from Trinklein, D.H. 2002. Lighting Indoor Plants. University of Missouri Extension Publication G 6515, University of Missouri-Columbia.
https://extension.missouri.edu/g6515.
High-Intensity Discharge (HID)
High-intensity discharge lamps are more costly to purchase and operate but have provided the highest quality light output options for many years. High-pressure sodium (HPS) lamps have been the most extensively used HID fixtures in commercial greenhouses. HPS lamps provide a large portion of yellow-orange light but are limited in the shorter, blue wavelengths. Metal halide (MH) lamps have a more balanced spectrum and may be preferred in completely controlled environments or growing conditions with high dependence on supplemented light.
MH lamps are sometimes used in combination with HPS lamps in greenhouses. The HPS lamps are slightly more efficient in transforming electric energy to light for plant growth than the MH lamps; they have, therefore, been recommended over MH lamps for supplemental light applications in commercial greenhouses. HPS lamps come in various suitable wattage levels, from 400 to 1,000 watts, for greenhouse applications. The choice of HPS lamp type and wattage is dependent on crop needs, available natural light and the greenhouse structure.
HID light fixtures have a bulb, reflector, ballast and capacitor (Picture 6). The bulb functions at a high temperature and becomes hot during operation, so it is
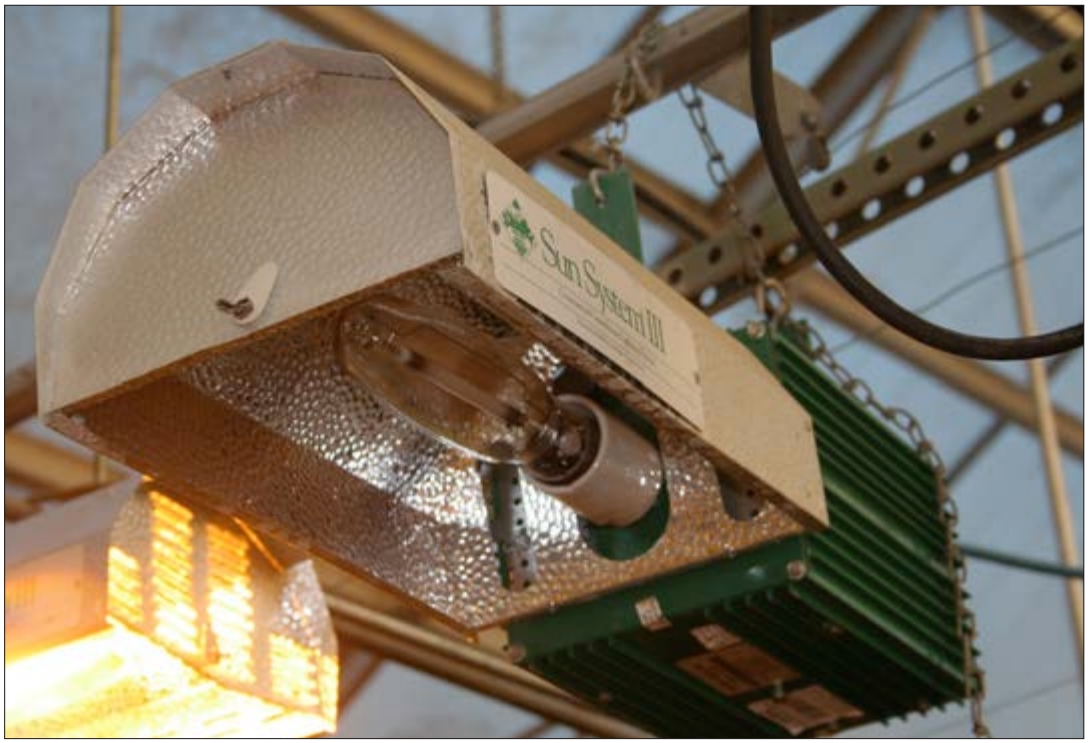
imperative to have good ventilation and place the bulbs at the proper distance from the plants. The design and placement of the lamp reflector is important for directing light onto the crop in a uniform pattern. The reflector design should also reduce the light directed into the fixture since additional heat can lead to premature bulb failure. Reflectors block natural light entering the greenhouse and sometimes severely reduce the amount of light reaching the crop. In an efficient greenhouse operation, light output is maximized uniformly across the crop and growing area. If some sections have lower levels of lights, plants in those areas may have slower development and grow taller, resulting in decreased and uneven overall plant quality. In a small greenhouse with limited opportunities for adequate clearance between the light fixtures and the plants, using large 1,000-watt fixtures to achieve uniform light can be challenging. Although it may be more costly to purchase several smaller lamps, multiple lights allow for more flexibility and opportunity to achieve uniform light dispersal. The layout of the lamps is dependent on the wattage choice (lamp intensity), fixture type, reflector shape and the distance between the reflector and the top of the crop. These criteria will determine the spacing needed between lamp fixtures, which will, in turn, determine how many lamps will be necessary to provide the desired amount of supplemental light.
Light-Emitting Diodes (LEDs)
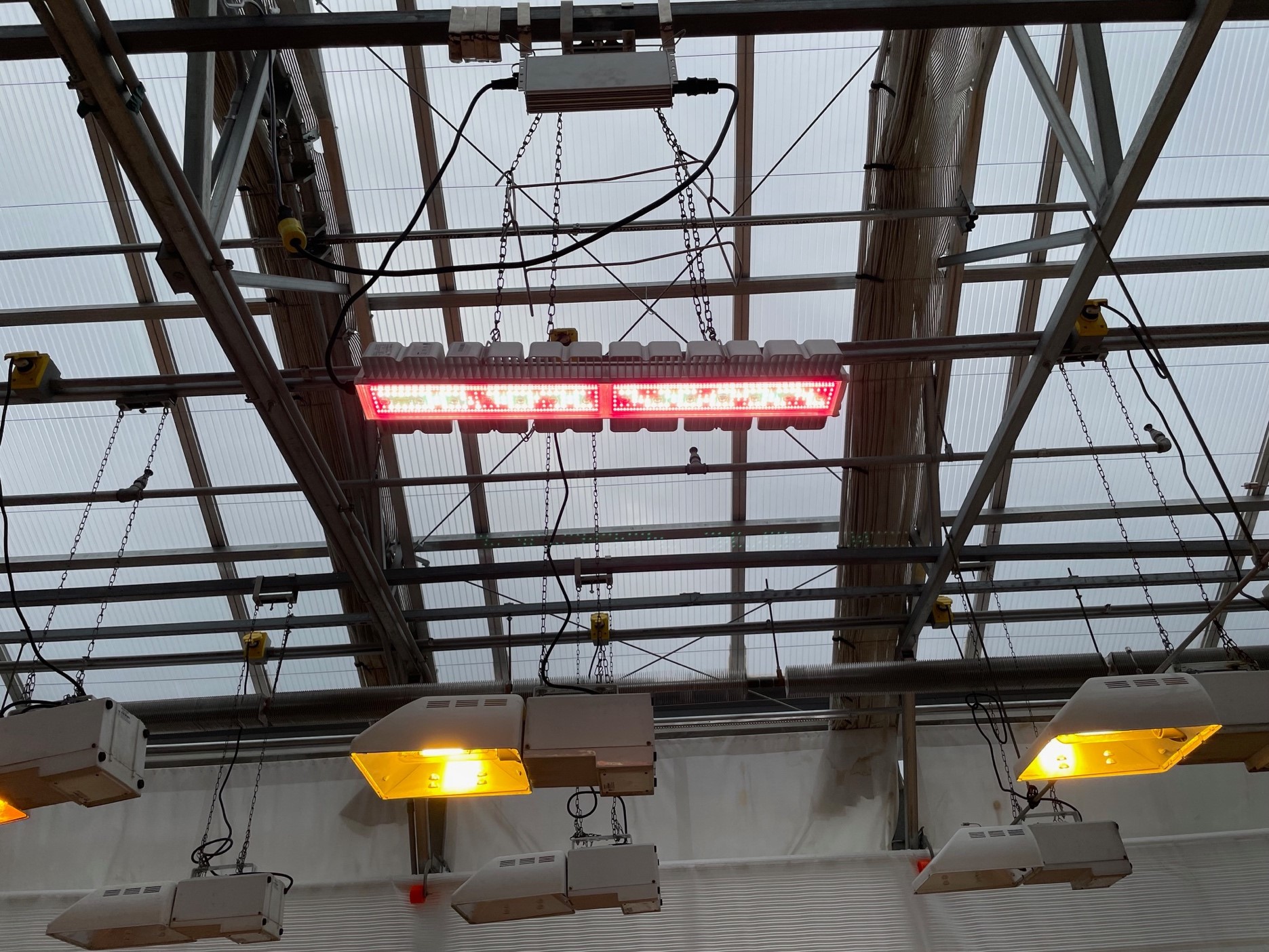
Light-emitting diodes are now available and used in various applications, including greenhouse lighting (Picture 7). An LED is a solid-state, light-emitting device that in comparison to traditional lighting sources, such as gas-filled pressurized bulbs, filaments and electrodes, allows extended hours of operation and potentially more efficient conversion of electric energy into light for plant growth or other applications. Individual LEDs are designed to emit a narrow spectrum or color of light, although white LEDs are also available.
The individual LEDs are arranged in arrays or panels with options to customize the overall light quality. Panels specifically designed for plant growth usually consist of LEDs that emit red, 630 to 660 nanometers (nm), and blue, 450 nanometers (nm), light. The primary reason for choosing these types of LEDs is the observed high rate of photosynthesis. Although red and blue light support photosynthesis, most plants have developed in a full spectrum of natural light. Growth under monochromatic light from LEDs in a controlled environment may modify plant development and flowering. Studies of growth and yield under the narrow light qualities of LEDs are ongoing, but remain limited to few plant species and growing environments. Monochromatic LEDs used for overhead supplemental lighting in a greenhouse can be expected to work well since even low levels of natural light are sufficient to complement the spectrum.
LEDs or similar technologies are becoming the major source for providing greenhouse lighting. Development of the LED technology is advancing with expectations of continued improvements in energy efficiency, light output and fixtures designed for greenhouse applications. Initially, the efficiencies of LEDs were similar to those of HID fixtures when based on light generated for photosynthesis and plant growth (Runkle et al., 2014)
The generation of light in LEDs does not produce heat in the beam of light, and LEDs are cool to the touch. Heat is generated at the fixture level, where it can be more easily dissipated. Reflectors are not necessary since the LED housing guides the light photons in one direction. Compared to HID lamps, LEDs can be placed closer to the plants, making high light intensity possible but reducing the distribution and area lighted. LED applications were initially implemented for use in plant factories, where crops are grown on shelves in several layers. Other applications are in seed and plant propagation, specialized production situations and high intensity production areas. LEDs have advantages in efficiency and longevity and may be designed and positioned to more precisely provide light for photosynthesis and other growth processes rather than flood light energy over the entire area of the greenhouse.
Day length
Plant Species | Crop Stage | Light Levels (Foot-candles 1 ) | Response 2 | Hours |
---|---|---|---|---|
African Violet | Cultivation | 900–1,200 | DN | 14 |
Alstromeria | Cultivation | 4,000–6,000 | LD | 13 |
Azalea | Propagation | 2,500–4,000 | --- | 16-18 |
Azalea | Cultivation | 3,000–4,000 | SD | 8 |
Begonia, Rieger | Cultivation | 2,000–3,500 | SD | 12 |
Begonia, Tuberous | Cultivation | 2,000–3,000 | LD | 12 |
Begonia, Wax | Cultivation | 3,000–5,000 | DN | 14 |
Bromeliads | Propagation | 3,000–5,000 | --- | 18 |
Bromeliads | Cultivation | 800–3,000 | DN | 18 |
Calceolaria | Cultivation | 2,000–3,500 | LD | 14-18 |
Chrysanthemum | Propagation | 3,000–5,000 | --- | 14 |
Chrysanthemum | Cultivation | 4,500–7,000 | SD | 10 |
Columbine | Propagation | 500–2,000 | LD | 13 |
Columbine | Cultivation | 3,000–4,000 | LD | 13 |
Cyclamen | Cultivation | 2,000–3,500 | DN | 14 |
Fuchsia | Cultivation | 2,000–4,000 | LD | 14 |
Geranium | Propagation | 2,500–4,000 | --- | 14 |
Geranium | Cultivation | 3,500–5,000 | DN | 14 |
Gerbera | 3,000–4,000 | SD | 12 | |
Impatiens | Cultivation | 2,500–4,000 | DN | 14 |
Kalanchoe |
Propagation | 2,000–4,000 | --- | 14 |
Kalanchoe |
Cultivation | 5,000–6,000 | SD | 11 |
Marigold, French |
Propagation | 4,000–6,000 | DN | 14 |
Marigold, African |
Propagation | 4,000–6,000 | SD | 12 |
Pansy |
Propagation | 3,000–5,000 | LD | 14 |
Petunia |
Propagation | 2,500–6,000 | LD | 16 |
Poinsettia |
Propagation | 1,000–2,000 | --- | 15 |
Poinsettia |
Cultivation | 4,000–6,000 | SD | 12 |
Snapdragon |
Cultivation | 3,000–6,000 | LD | 18 |
Sunflower | Cultivation | 3,000–5,000 | SD or DN | 14 |
Herbs and Vegetables | Crop Stage | Light Levels (Foot-candles 1 ) | Response 2 | Hours |
---|---|---|---|---|
Basil | Production | 3,000–5,000 | SD or DN | 16 |
Bell Pepper
|
Production | 4,000–5,000 | DN | 14 |
Cabbage transplants
|
Propagation | 3,000–5,000 | DN | 16 |
Cucumber
|
Propagation | 1,000–2,500 | --- | 14 |
Cucumber
|
Production | 3,500–4,500 | DN | 14 |
Dill
|
Propagation | 3,000–4,000 | LD | 12 |
Dill
|
Flowering | 3,000-4,000 | LD | 16 |
Lettuce
|
Production | 1,500-2,500 | LD | 14 |
Mint
|
Production | 4,000-5,000 | SD | 14 |
Oregano
|
Production | 3,000-5,000 | DN | 14 |
Parsley
|
Production | 4,000-5,000 | DN | 14 |
Rosemary
|
Production | 5,000-7,000 | DN | 14 |
Strawberry |
Propagation | 1,500-2,500 | --- | 16 |
Strawberry
|
Production | 4,000-6,000 | LD or DN | 11-16 |
Thyme
|
Production | 6,000-7,000 | LD | 10 |
Tomato
|
Propagation | 1,000-2,500 | --- | 16 |
Tomato |
Production | 4,000-5,000 | DN | 16 |
1Foot-candles: a foot-candle is how bright the light is one foot away from the source.
2DN, LD, SD: Plants flower in response to the day length. A long-day (LD) plant flowers
when the day is longer and a short-day (SD) plant when the day is shorter than a certain
time. Day neutral (DN) plants flower at any day length.
Source: Adapted from Currey, C.J., R.G. Lopez and N.S. Mattson. 2011. Flower Induction of Annuals. Purdue Extension HO-249-W (www.extension.purdue.edu/extmedia/HO/HO-249-W.pdf); Dole, J.M. and H.F. Wilkins. 2005. Floriculture, Principles and Species, 2nd Ed.
Pearson Prentice Hall, Upper Saddle River, New Jersey; and Hamrick, D. 2003. Ball
Redbook, Vol. 2, Crop Production, 17th Ed. Ball Publishing, Batavia, Illinois
Lighting Choices
Plant growth and photoperiodic control have different supplemental lighting requirements. The photoperiod or day-length requirements depend on the plant species (Table 11). In Alaska, with naturally large variations in day length (Table 12), attention to photoperiod is especially important. The day length can easily be increased in a greenhouse environment using a light source with low intensity output and an adjustable 24-hour timer. Incandescent bulbs with simple reflectors spaced 4 feet apart above the plants, have been used extensively to lengthen the day (Bartok, 2000). LEDs with a more balanced spectrum are now available and replacing incandescent bulbs and CFLs for extending the day to induce flowering in long day plants or prevent flowering in short day plants.
Shortening the natural day can be accomplished by covering the plants and the growing area with a blackout material for the required number of hours each day. Some plants are highly sensitive to light pollution during the dark period. Even very limited light of 1 or 2 footcandles may interrupt the perception of dark. During natural short days, light from sources such as street, traffic or emergency lights can interrupt and interfere with the daily dark period.
Month | Fairbanks | Anchorage | Kenai |
---|---|---|---|
January | 5.3 | 6.6 | 6.7 |
February |
8.5 | 9.1 | 9.1 |
March |
11.8 | 11.9 | 11.9 |
April |
15.3 | 14.8 | 14.7 |
May |
18.8 | 17.5 | 17.4 |
June |
21.4 | 19.2 | 18.9 |
July |
19.9 | 18.3 | 18.1 |
August |
16.4 | 15.8 | 15.6 |
September |
13.0 | 12.9 | 12.8 |
October |
9.6 | 10.0 | 10.0 |
November |
6.3 | 7.3 | 7.4 |
December |
4.0 | 5.6 | 5.9 |
Adapted from 2024 Astronomical Applications Department, U.S. Naval Observatory, Washington, D.C.
When the main purpose of supplemental lighting is to enhance plant growth, several factors need to be considered, such as crop requirements, desired intensity and quality, uniformity (number of required fixtures), operating costs and financial return on the investment. Several units and methods are used to measure available light. Foot-candles are a common measurement unit of light. Foot-candles and the unit “lux,” commonly used in Europe, are both based on the detection of visual light or brightness by the human eye. For crop growth, however, the photosynthetic active radiation (PAR) in the 400 to 700 nm range is of primary interest. PAR levels can be measured in several units, including foot-candles, although the most appropriate unit for plant growth is micro-mol (µmol) per square meter (m2) and second (s), or µmol·m-2·s-1. This quantum, or photon, unit measures the number of photons or light particles that appear on one square meter (10.8 square feet) every second. Another common light and PAR unit is watt per square meter (W/m2) for measuring the energy in the photons falling on one square meter each second. PAR unit conversions for sunlight, HPS, metal halide, fluorescent and incandescent light sources are offered in Table 13. Conversions for light measurements under LEDs vary widely with the type and spectrum of the LED fixtures.
Instantaneous light measurements are helpful in showing the amount of available light at the time the reading is made. Since natural light is continuously changing during the day, a single measurement may not give a good indication of the total daily light available for crop growth. Therefore, the total amount of light provided during a day is expressed as the daily light integral (DLI). The DLI is a measure of the number of light particles or photons available to plants during 24 hours, or a day.
The commonly used unit for DLI is moles per square meter and day, or mol·m-2·day-1. Plant growth, development, rate of maturation, yield and quality depend on DLI and provide information for determining when supplemental lighting or shading may be needed. During the long days of the Alaska summer, the natural DLI often reaches 60 mol/m2 and day, while in the winter DLI often drops below 2 mol/m2 and day.
Table 13. Converting Light Measurements from One Unit to Another | ||||||||
Conversion of 1 µmol.m-2.s-1 | ||||||||
---|---|---|---|---|---|---|---|---|
Unit | Type of Measurement | Main use | Sunlight | HP Sodium | Metal Halide |
CW fluorescent |
Incandescent (100 W) |
Light emitting diodes |
Footcandles | Visible (human eye) | Industry (U.S.) | 5.02 | 7.62 | 6.60 | 6.87 | 4.65 | Varies by product |
Lux | Visible (human eye) | Industry (Europe) | 54 | 82 | 71 | 74 | 50 | Varies by product |
µmol.m-2.s-1 of PAR | Quanta of light in PAR range | Horticulture research, industry | 1 | 1 | 1 | 1 | 1 | 1 |
mol.m-2.d-1 of PAR |
Daily light integral (DLI): accumulated PAR over the entire day | Horticulture research, industry | Average µmol.m-2.s-1 x60sec/min x 60 min/hr x hours) / 1,000,000 | |||||
W.m-2 (PAR) |
Energy in PAR range | Engineers, research | 4.57 | 4.98 | 4.59 | 4.59 | 5.00 | Varies by product |
W.m-2 (total) | Total energy | Engineers, research |
0.51 | 0.56 | 0.59 | 0.54 | 2.58 | Varies by product |
Adapted from Lopez and Runkel, 2017. Light Management in Controlled Environments. |
Incandescent | Fluorescent | HP sodium | Metal halide | |
---|---|---|---|---|
Light Source |
150W | F40CW/40W | 400W | 400W |
Total Input (W)
|
150 | 48 | 440 | 425 |
Lamp Flux (lm)
|
2,850 | 3,150 | 48,000 | 31,500 |
Effective Flux (lm)*
|
___ | ___ | 38,400 | 25,200 |
Lamp Flux (mW)
|
11,970 | 9,135 | 110,400 | 88,200 |
Conversion Factor (mW/lm)
|
4.2 | 2.9 | 2.3 | 2.8 |
Effective Flux (mW)* |
___ | ___ | 88,300 | 70,600 |
*The effective flux is assumed to be approximately 80% of the lamp flux for the two
HID lamps. It can vary from a low of less than 50% to a high of 70% for incandescent
and fluorescent lamps, depending on reflectors.
Source: Adapted with permission from Poot, J. 1984. Application of Grow lights in Greenhouses and Horticultural Lighting, Philips Lighting Co., Somerset, N.J.
The selection of light fixtures for supplemental lighting depends on how they are to be used. First, consider the minimum light requirement for producing a certain crop (Table 11), then find out the energy values for the intended light fixtures (Table 14).
To determine the required number of lamp fixtures, multiply the desired light level by the illuminated area and then divide this by the effective flux of the selected light source. The effective flux is approximately 80 percent of the rated flux for HID lamps. For incandescent and fluorescent lamps, effective flux varies from 50 to 70 percent depending on the type of reflector.
Growing lettuce seedlings at a light level of 25 watts per square meter (960 foot-candles) in a 1.5- by 3-meter area (4.5 square meters, or 48.4 square feet) would require a total of 25 watts per square meter multiplied by 4.5 square meters, or 112.5 watts of light. If using 400-watt HPS lamps, the effective flux is 38.4 (Table 14). The number of light fixtures needed to provide the desired light level for the 4.5-square meter area is 112.5 watts divided by 38.4, which equals 2.93, or three 400-watt HPS fixtures. The cost for operating HID lamps can be high when several hours of supplemental lighting are required. Before deciding whether to install light fixtures, consider the purchase and operating costs. The daily cost for electric power can be estimated by multiplying the wattage of the fixture by the hours of operation and the hourly electric cost.
To determine the electric cost, refer to a recent electric bill and divide the total cost by the number of kilowatthours (kWh) used. For example, if the monthly electric bill is $130 for 650 kWh, the average cost per kilowatthour is 20 cents ($130/650 = $0.20/kWh). For the lettuce-seedling example, three 400-watt HPS fixtures are needed for the 4.5-square meter (48.4-square foot) growing area. Each lamp fixture requires an additional 40 watts for the ballast (Table 10), so you would use a total of (400 watts + 40 watts) × 3 fixtures for 1,320 watts per kilowatt-hour (or 1.32 kW per kWh). If light is supplemented for 12 hours each day, the operating cost can be estimated by multiplying 1.32 kW by $0.20/kWh and 12 hours, which equals $3.17 per day.
Control Systems
Heating, cooling, humidity and light levels all interact in determining the greenhouse environment. Although control systems can be simple on-and-off switches, more sophisticated approaches that take advantage of computers to improve the overall control release the greenhouse operator from constantly having to monitor and make adjustments. The placement of sensors in the greenhouse is critical. To get accurate readings and maintain the desired conditions for the crop, sensors should be located at plant canopy height in an area with limited direct influence from heaters, vents, fans or drafts. Sensors should also be shielded from direct sun to ensure accurate measurements of air temperatures and humidity.
Thermostats
Mechanical thermostats have been used extensively in greenhouses and are usually cheaper than controllers. Thermostats operate with a temperature-sensitive liquid in a coiled tube. As the temperature increases, the liquid expands in the tube, activating a switch that turns a fan on. As temperatures drop, the liquid within the thermostat cools and retracts, shutting off the fan switch. In a high-low thermostat, the liquid will continue to retract in the coiled tube as temperatures drop, until it activates another low temperature switch that can be used to turn on a heating unit within the greenhouse. Most thermostats are accurate to within 5°F to 6°F of switch activation. Transistorized thermostats are more expensive than mechanical ones, but are more accurate, usually within 1°F.
Thermostats and sensors for temperature and humidity should be shielded from direct sunlight and preferably aspirated. A thermostat placed in direct sun will give excessively high readings on sunny days. The various sensors and thermostats need to be located close together, preferably at crop height and away from heaters, fans and air intakes.
Choose thermostats that are valued in two-degree increments. Home-type thermostats (comfort zone markings) do not offer good greenhouse control. Place at least one thermometer by the thermostat to determine its accuracy. Any discrepancies should be noted and the thermostat adjusted accordingly to achieve desired temperature set points. Be sure to use the correct thermostats for cooling and heating. A good cooling thermostat set at 70°F should turn on at 72°F and off at approximately 68°F, while a heating thermostat set at 70°F should turn on at about 68°F and off at 72°F.
One of the biggest challenges for Alaska greenhouse owners is to properly coordinate the cooling and heating systems to avoid system overlap (cooling while heating or heating while cooling). System overlap can be especially difficult in smaller greenhouses when trying to vent at very cold outside temperatures or heat using heaters that generate excessive heat. Maintaining a desired temperature under these scenarios will cause the equipment to work simultaneously if the temperature heating and cooling set points are too close. Unfortunately, having controllers or thermostats with set points too far apart will result in erratic up and down temperatures. Adjustments, observations and time will be required to find the best combination of control points to optimize the heating and cooling capabilities of the greenhouse. If system overlap is a concern, the use of multiple exhaust fans with adjustable speeds and regulated by separate thermostats may be necessary to reach acceptable greenhouse control.
Controllers
A controller is an electronic device capable of continuously monitoring the greenhouse environment. The controller can independently activate different pieces of equipment (fans, heaters, shade curtains) and coordinate equipment use to eliminate system counteractions and overlap problems. Simple units are available to monitor temperature and ventilation needs, while more advanced models can handle additional functions such as irrigation, lighting and programming for special conditions. Controllers are usually compact, waterproof units that give good service over a wide range of environmental conditions. Installation may also be relatively simple as relays, switches and controllers are already wired and connected together.
Although controllers will help in eliminating system overlaps, venting and heating equipment may not respond sufficiently fast to improve environmental control, especially under Alaska’s cold air conditions. Other factors, such as wind and rapidly changing cloud and sun patterns, will also affect the operation of the equipment and the ability of the controller to maintain a consistent and uniform greenhouse environment.
Close attention to the environment will improve crop performance and reduce some of the initial frustrations commonly encountered with greenhouses. This publication offers some suggestions to consider for successfully managing your greenhouse. You will find as you gain experience that greenhouses can be extremely productive and efficient, even in the challenging environment of Alaska.
References
Astronomical Applications Department. 2024. U.S. Naval Observatory, Washington, D.C. 20392-5420 (http://aa.usno.navy.mil/data/index).
Bartok, J.W., D.S. Ross, J. White, W.J. Roberts, C.A. Aldrich and R.A. Parsons. 1982. Solar Greenhouses for the Home, NRAES-2. Ithaca, New York. Natural Resource, Agriculture and Engineering Service (out of print).
Bartok, J.W. 2000. Greenhouses for Homeowners and Gardeners, NRAES-137. Ithaca, New York. Natural Resource, Agriculture and Engineering Service.
Bartok, J.W. 2001. Energy Conservation for Commercial Greenhouses, NRAES-3, 2001 Revision. Ithaca, New York. Natural Resource, Agriculture and Engineering Service
Bellows, B. 2011. Solar Greenhouses. Updated by D. Ryan and T. Hinman, Sustainable season extension: considerations for design. ATTRA National Sustainable Agriculture Information Service. Publication IP416. (https://attradev.ncat.org/wp-content/uploads/2022/06/seasonextension.pdf).
Currey, C.J., R.G. Lopez and N.S. Mattson. 2011. Flower Induction of Annuals. Purdue Extension HO-249-W (www.extension.purdue.edu/extmedia/HO/HO-249-W.pdf).
Dole, J.M. and H.F. Wilkins. 2005. Floriculture, Principles and Species, 2nd ed. Upper Saddle River, New Jersey: Pearson Prentice Hall.
Fisher, P. and E. Runkle. 2004. Lighting Up Profits: Understanding Greenhouse Lighting. Willoughby, Ohio: Meister Publishing Co.
Grainger, Inc. 2014. Catalog 405: 4094. (www.grainger.com/content/cat_405_ventilation).
Hamrick, D. 2003. Ball Redbook, Volume2: Crop Production, 17th ed. Batavia, Illinois: Ball Publishing.
Kramer, J. 2013. “Greenhouse Heating.” Association of Education and Research Greenhouse Curators, AERGC Newsletter 25(1): 4-7.
Lopez, R. and E.S. Runkle. 2017. Light management in controlled environments. Willoughby, Ohio: Meister Media Worldwide.
Nelson, P.V. 2012. Greenhouse Operation and Management, 7th ed. Upper Saddle River, New Jersey: Pearson Prentice Hall.
Runkle, E. and A.J. Both. 2011. Greenhouse Energy Conservation Strategies. Michigan State University Extension Bulletin E-3160. East Lansing, Michigan.
Runkle, E., J. Nelson and B. Bugbee. 2014. “LEDs vs. HPS Lamps: A Reality Check.” Greenhouse Product News 6:54.
Trinklein, D.H. 2002. Lighting Indoor Plants. University of Missouri Extension Publication G 6515. University of Missouri-Columbia. (https://extension.missouri.edu/g6515).
Acknowledgements
The authors would like to thank John W. Bartok, Jr., Extension professor emeritus, Department of Natural Resources Management and Engineering, University of Connecticut; Ron Sexton, owner, Trinity Greenhouse, Kenai, Alaska; and Thomas R. Jahns, former Extension faculty, Agriculture and Horticulture, University of Alaska Cooperative Extension Service, for their input and review in the development of this publication. We would also like to thank Natural Resource, Agriculture and Engineering Service for allowing us to reprint selected tables and figures.
To simplify information, trade names of products have been used. No endorsement of named products by the University of Alaska Fairbanks Cooperative Extension Service is intended, nor is criticism implied of similar products that are not mentioned. All photos, artwork and figures UAF Extension, unless otherwise noted.
Meriam Karlsson, Professor of Horticulture, Institute of Agriculture, Natural Resources and Extension. Originally prepared by Wayne Vandre, former Extension Horticulturist.
Reviewed October 2019