The greatest story of man and permafrost
The greatest story of man and permafrost
Submitted by Ned Rozell
Phone: 907-474-7468
07/16/08
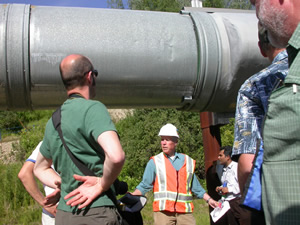
In 1973, Elden Johnson was a young engineer working on one of the most ambitious and uncertain projects in the world--an 800-mile steel pipeline that carried warm oil over frozen ground. Thirty-five years later, Johnson looked back at what he called "the greatest story ever told of man’s interaction with permafrost."
Strung over and beneath the surface of Alaska from Prudhoe Bay to Valdez, the trans-Alaska pipeline, at 31 years old, is entering its second lifetime. The four-foot in diameter, half-inch-thick steel pipe had an original design lifespan of 30 years. The State of Alaska and the U.S. Department of the Interior recently gave the pipeline the green light for another 30 years of operation.
"It’s like a car," said Johnson, who works for Alyeska Pipeline Service Company, while standing under the pipeline near Fairbanks during a recent permafrost conference lecture. "As long as you maintain it, it’ll continue to work."
Permafrost, frozen ground that is a relic of the last ice age, exists beneath about 75 percent of the pipeline’s 800-mile route. When ice-rich permafrost thaws, the ground slumps, causing problems for structures above.
After the 1969 oil discovery at Prudhoe Bay, developers unfamiliar with Alaska wanted to bury the entire supply of Japanese-made pipe. After a review by people who knew the dangers of building on permafrost, a legion of workers constructed a pipeline buried for 380 miles and--in areas of permafrost--built above the ground on platforms for 420 miles.
The initial design was good, but not perfect, Johnson said. He remembered during construction when he and others were inspecting the ground from the Yukon River to Coldfoot. They found unstable permafrost and recommended re-design of sections of the pipeline. Instead of conventional buried pipeline, the engineers called for more expensive and time-consumptive, above-ground pipeline.
"We changed the design for at least 20 percent of that distance," he said. "They were gut-wrenching decisions potentially impacting the startup schedule."
The call to elevate more than half the pipeline turned out to be a good one. Even though engineers bored holes in the ground about every 800 feet to check for permafrost, they didn’t find it all. When the pipeline was two years old in 1979, the pipe buckled and leaked in two buried sections because of thawed permafrost. In both cases, the pipeline, which carried oil that left the ground in Prudhoe Bay as warm as 145 degrees Fahrenheit, caused about four feet of settlement. Engineers fixed those and other problems. The two leaks in 1979 are still the only spills caused by permafrost.
Alyeska workers check the pipeline each year for signs of settling and proper operation of the heat pipes that help keep the support posts of the above-ground pipeline anchored in frozen ground. The buried pipeline has become more stable over its 31 years as the rapid thawing of early years has settled down.
"The risk to the buried pipeline right now is becoming minimal," Johnson said.
The pipeline has delivered more than 16 billion barrels of oil since its startup in June 1977, with two brief shutdowns due to permafrost. Johnson estimated permafrost-related maintenance has totaled about 5-to-10 percent of the operating costs over the life of the pipeline.
"It’s the cost of doing business in the Arctic," he said
With a career of work on the massive engineering project Johnson calls "a beautiful thing," he is retiring from Alyeska this winter. His mind won’t stray far from the challenges of building pipelines across cold country. His daughter Katie, a mechanical engineering graduate from the University of Alaska Fairbanks, has just signed on to help work with the natural gas pipeline from the North Slope southward.
"It’s kind of a second-generation opportunity to look at the next pipeline," Johnson said.
This column is provided as a public service by the Geophysical Institute, University of Alaska Fairbanks, in cooperation with the UAF research community. Ned Rozell is a science writer at the institute.