PPE Emission Testing Wins Top Nanook Award
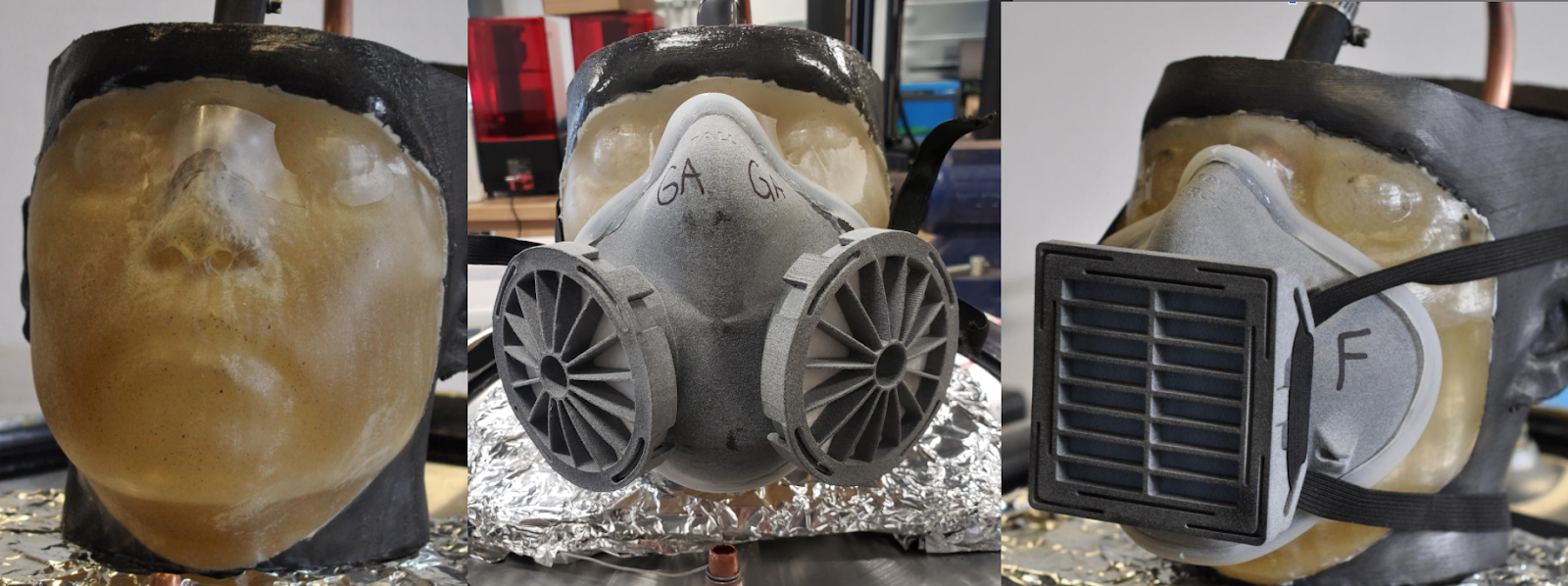
Well-established standards exist for testing and quantifying how well masks and filters protect a user from environmental dangers. But what about the reverse — how well do masks and filters protect others from aerosols produced by the wearer?
UAF Institute of Northern Engineering’s Orion Lawlor, with support from ACEP’s Dayne Broderson, devised a way to answer that question. Their apparatus won the top staff-led innovation in the 2019-2020 UAF IDEAs award competition.
The Innovative Disclosures and Entrepreneurial Activities awards, hosted by the UAF Office of Intellectual Property and Commercialization, recognize innovative solutions from submitted invention disclosures from UAF and University of Alaska Southeast for the academic year.
The testing apparatus is a sealed chamber with an aerosol generator emitting through a testing head’s nostrils. The testing head has three major components: a 3D-printed structure that provides standard rigidity where human skulls, cheek bones, and jaws would provide rigid structure; a nostril and nose path for the aerosols to be emitted from; and a gelatin molded face to flesh out from the skeleton structure, giving a more realistic mask-to-face fit where there is a mix of rigid and flexible surfaces.
An aerosol sensor measures the chamber’s general aerosol levels. Known levels of aerosols are pumped through the testing head’s nostrils, which are covered with a mask or filter, and into the chamber. Measurements can then quantify the reduction of aerosol emissions by different masks and filters.
This methodology, equipment and testing was developed as part of an Immediate Innovation for Coronavirus project with funding from the UAF Center for Innovation, Commercialization and Entrepreneurship and the U.S. Office of Naval Research.
For more information on the testing apparatus or protocol, contact Orion Lawlor at lawlor@alaska.edu.
Testing head with 3d printed structure and gelatinous face mold. Shown with two mask prototypes sent for testing by the Naval Undersea Warfare Center Keyport's additive manufacturing team. Photos by Orion Lawlor.